Are you frustrated with compressors that promise savings but deliver inflated power bills? You’re not alone. 63% of manufacturers overpay for compressed air due to poor system matching (U.S. DOE). The truth is: off-the-shelf “energy-efficient” compressors often fail when faced with real-world variables like fluctuating demand, altitude, or production shifts.
Meet Seize Air’s 3-Pillar Solution – where precision engineering meets AI-driven optimization to eliminate wasted energy and boost ROI.
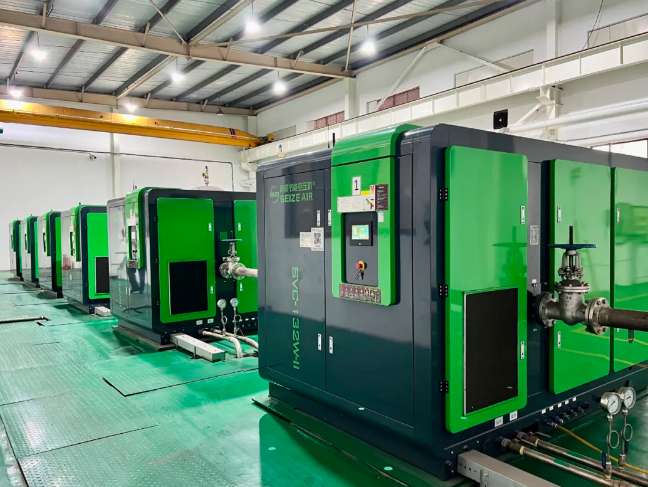
The Hidden Costs of Generic “Energy-Saving” Compressors
Before exploring solutions, Seize Air bespoke engineering let’s dissect why most compressor upgrades underperform:
- “One-Size-Fits-All” Deception
- 41% of plants use compressors oversized by 20-35% (Compressed Air Challenge)
- Mismatched pressure bands waste 1-3% energy per unnecessary PSI
- Reactive Maintenance Traps
- Undetected leaks drain 20-30% of airflow
- 85% of failures occur due to unmonitored vibration/temperature spikes
- Hidden Ownership Costs
- 80% of TCO comes from energy/maintenance – not purchase price
Real-World Impact: A Midwest auto parts plant spent $218,000 annually on a “high-efficiency” compressor that operated at 42% load efficiency.
Seize Air bespoke engineering Against Energy Waste
🔰 Advantage 1: Laser-Targeted Custom Engineering – No More Guesswork
Forget generic specs. Seize Air’s ISO 50001-certified engineers conduct a 72-Point Plant Audit to map your true air needs:
✅ Demand Profiling:
- 24/7 airflow monitoring with Class 1 (±1%) ultrasonic sensors
- Peak/off-peak pressure mapping (0.1-bar resolution)
✅ Process-Specific Optimization:
- Injection molding: Eliminate pressure drops during tool changes
- Packaging lines: Sync with intermittent valve actuation
✅ Climate & Site Adaptations:
- Altitude compensation (tested up to 4,500m)
- Humidity/temperature-adjusted cooling
Case Study: A Brazilian beverage plant reduced energy costs by 31% after Seize Air redesigned their system around seasonal production spikes.
🔰 Advantage 2: Smart IoT Guardian – Real-Time Optimization
Seize Air’s proprietary SmartMaster 4.0 platform transforms compressors into self-optimizing assets:
Live Monitoring Dashboard:
- Energy consumption per cubic meter (kWh/Nm³)
- Leakage rate alerts (detects <0.5 CFM losses)
- Motor efficiency tracking (IE5 standards)
Predictive Power:
- Forecast maintenance needs via ML algorithms (92% accuracy)
- Auto-adjust pressure bands during shift changes
Remote Control:
- Adjust airflow from your phone during emergencies
- Multi-compressor orchestration for large facilities
Result: A German chemical plant achieved 24/7 ±0.2-bar stability, cutting scrap rates by 18%.
🔰 Advantage 3: Built-to-Last Performance – No Compromises
Customization ≠ fragility. Seize Air’s military-grade engineering ensures your system thrives:
Core Innovations:
- Dual Armor® Screw Rotors: Tungsten-carbide coated for 50,000+ hour lifespan
- Zero-Leak Valves: Aerospace-grade seals tested to 500,000 cycles
- CyberSafe™ Control: Hack-resistant firmware (IEC 62443 certified)
Tested to Extremes:
- 100% DOD (Depth of Discharge) testing for variable loads
- Salt spray resistance (500+ hours per ASTM B117)
Maintenance Edge:
- Tool-free filter swaps (3-minute design)
- QR-code guided troubleshooting
How Our Process Guarantees Results
Step 1: Free Plant Energy Health Check
- 48-hour airflow audit with temporary sensors
- 15-page report detailing savings opportunities
Step 2: Custom System Simulation
- Digital twin modeling using FluidFlow® software
- ROI projections with/without upgrades
Step 3: Turnkey Installation
- Seize Air-certified technicians handle:
- Pipe routing optimization
- Heat recovery integrations
- Staff training
Step 4: Lifetime Performance Guardianship
- Annual efficiency checkups
- Priority 24/7 support (global hotline)
Industry-Proven Success Stories
🏭 Food Packaging Leader Saves $1.2M
Challenge: 57% energy waste from outdated multi-compressor setup
Seize Air Solution:
- Installed 2×375kW PM VSD compressors with centralized SmartMaster
- Repurposed waste heat for sterilization tunnels
Result: 34% lower energy bills, 14-month ROI
🏭 Aerospace Manufacturer Eliminates Downtime
Challenge: Oil contamination risk in composite curing
Seize Air Solution:
- ISO 8573-1 Class 0 oil-free compressors
- Smart pressure compensation for autoclaves
Result: Zero defect-related recalls, 99.6% uptime
Your Custom Energy-Saving Roadmap Starts Here
Limited Offer: First 20 respondents receive:
- Free UL-certified power quality analysis ($2,500 value)
- Free 3D compressed air system rendering
[Claim My Free Plant Audit Now]
FAQ Section
Q: How long does customization take?
A: Most bespoke systems ship within 4-6 weeks post-audit.
Q: Can retrofits work with existing compressors?
A: Yes! Our SmartMaster retrofit kits upgrade legacy units in 48 hours.
Q: What industries do you specialize in?
A: Pharmaceuticals (GMP), automotive (IATF 16949), textiles, and mining.
ℹ️Website: www.szaircompressor.com
☎️WhatsApp:https://wa.me/8615001719145
📧email:info@seize-air.com
发表回复